Manufacturing Automation Platform
In today's rapidly evolving industrial landscape, the integration of a Manufacturing Automation Platform (MAP) is becoming increasingly essential for companies aiming to enhance efficiency and competitiveness. By streamlining production processes, reducing human error, and optimizing resource management, MAPs empower manufacturers to meet the demands of modern markets. This article explores the transformative impact of automation platforms on manufacturing operations and highlights key benefits and considerations for implementation.
Introduction to Manufacturing Automation Platforms (MAPs)
Manufacturing Automation Platforms (MAPs) are revolutionizing the industrial landscape by integrating advanced technologies to streamline production processes. These platforms offer a comprehensive suite of tools designed to optimize efficiency, reduce human error, and enhance productivity across various manufacturing sectors. By leveraging real-time data and analytics, MAPs enable manufacturers to make informed decisions, ultimately leading to improved operational performance and cost savings.
- Seamless integration with existing systems
- Real-time monitoring and data analytics
- Enhanced scalability and flexibility
- Reduction in operational costs
- Improved quality control and compliance
As industries continue to evolve, the adoption of MAPs becomes increasingly crucial for maintaining a competitive edge. These platforms not only facilitate the automation of repetitive tasks but also empower companies to adapt to changing market demands with agility. By embracing MAPs, manufacturers can achieve a higher level of precision and efficiency, paving the way for innovation and growth in the ever-evolving industrial landscape.
Key Features and Benefits of MAPs
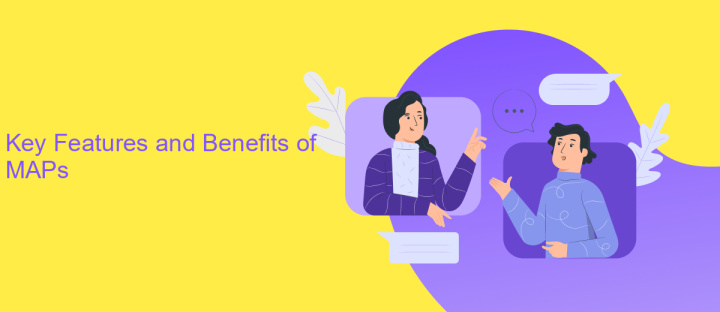
Manufacturing Automation Platforms (MAPs) are designed to streamline production processes by integrating advanced technologies and optimizing workflows. One of the key features of MAPs is their ability to facilitate real-time data collection and analysis, enabling manufacturers to make informed decisions quickly. This enhances operational efficiency by reducing downtime and minimizing waste. Additionally, MAPs often include predictive maintenance tools, which help anticipate equipment failures before they occur, thus ensuring continuous production and reducing unexpected costs.
Another significant benefit of MAPs is their flexibility in integrating with existing systems and third-party applications. Services like ApiX-Drive play a crucial role here by providing seamless integration capabilities, allowing manufacturers to connect various software solutions without extensive coding. This simplifies the process of automating tasks and ensures that all systems work harmoniously. Furthermore, MAPs contribute to improved product quality by maintaining consistent production standards and enabling precise control over manufacturing parameters. Overall, the adoption of MAPs leads to increased productivity, cost savings, and a competitive edge in the market.
Types of Manufacturing Automation Platforms
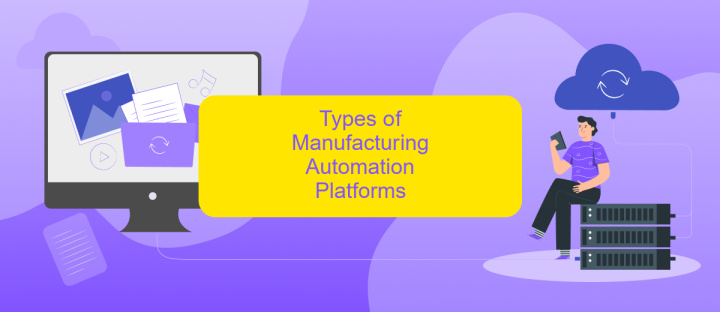
In the realm of modern manufacturing, automation platforms play a pivotal role in enhancing productivity and efficiency. These platforms integrate various technologies to streamline production processes, reduce human error, and optimize resource utilization. Understanding the different types of manufacturing automation platforms is crucial for selecting the right solution tailored to specific industrial needs.
- Fixed Automation: This type focuses on high-volume production with a dedicated system for specific tasks, offering low flexibility but high efficiency.
- Programmable Automation: Suitable for batch production, this platform allows reprogramming for different tasks, providing moderate flexibility and efficiency.
- Flexible Automation: Designed for varied production tasks, it offers high flexibility, enabling quick adaptation to new product designs without significant downtime.
- Integrated Automation: This comprehensive system combines various automated processes, allowing seamless coordination and control across the entire production line.
Each type of manufacturing automation platform offers unique advantages and is suited to different production environments. Fixed automation is ideal for mass production, while flexible automation caters to dynamic manufacturing needs. Understanding these distinctions helps businesses make informed decisions, ultimately leading to improved operational outcomes and competitive advantage in the market.
Implementing a Manufacturing Automation Platform
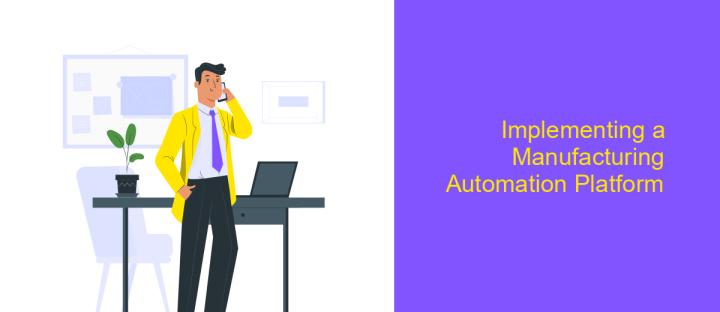
Implementing a manufacturing automation platform requires careful planning and strategic execution. The first step involves assessing the current manufacturing processes to identify areas where automation can bring the most significant benefits. This evaluation helps in understanding the specific needs and challenges that the platform must address.
Once the assessment is complete, selecting the right technology and tools becomes crucial. This involves researching various automation solutions and choosing one that aligns with the company's goals, budget, and technical capabilities. Collaboration with technology vendors and industry experts can provide valuable insights during this phase.
- Conduct a thorough needs analysis to determine automation requirements.
- Select appropriate technologies and tools for implementation.
- Engage stakeholders and ensure alignment with business objectives.
- Develop a detailed implementation plan with clear timelines and milestones.
Finally, a phased implementation approach is advisable to minimize disruptions. Pilot testing the platform on a smaller scale allows for adjustments and refinements before a full-scale rollout. Continuous monitoring and feedback collection ensure the platform evolves to meet changing needs and maximizes efficiency gains.

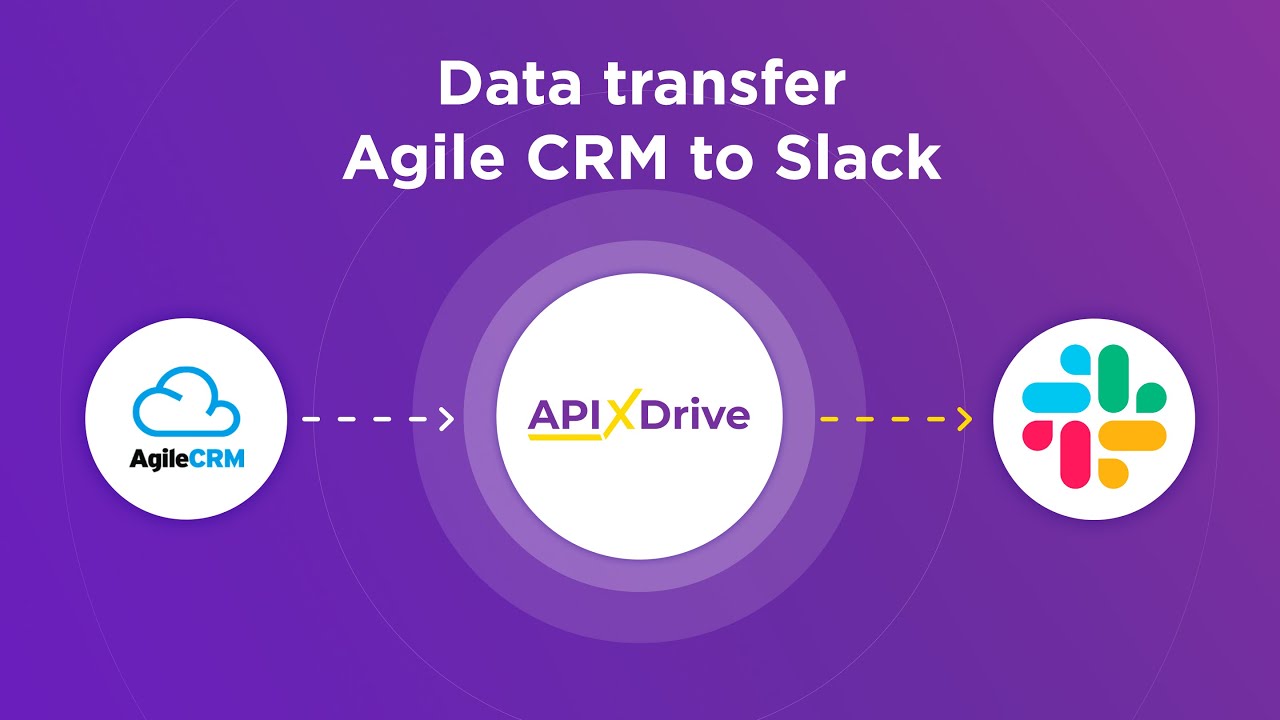
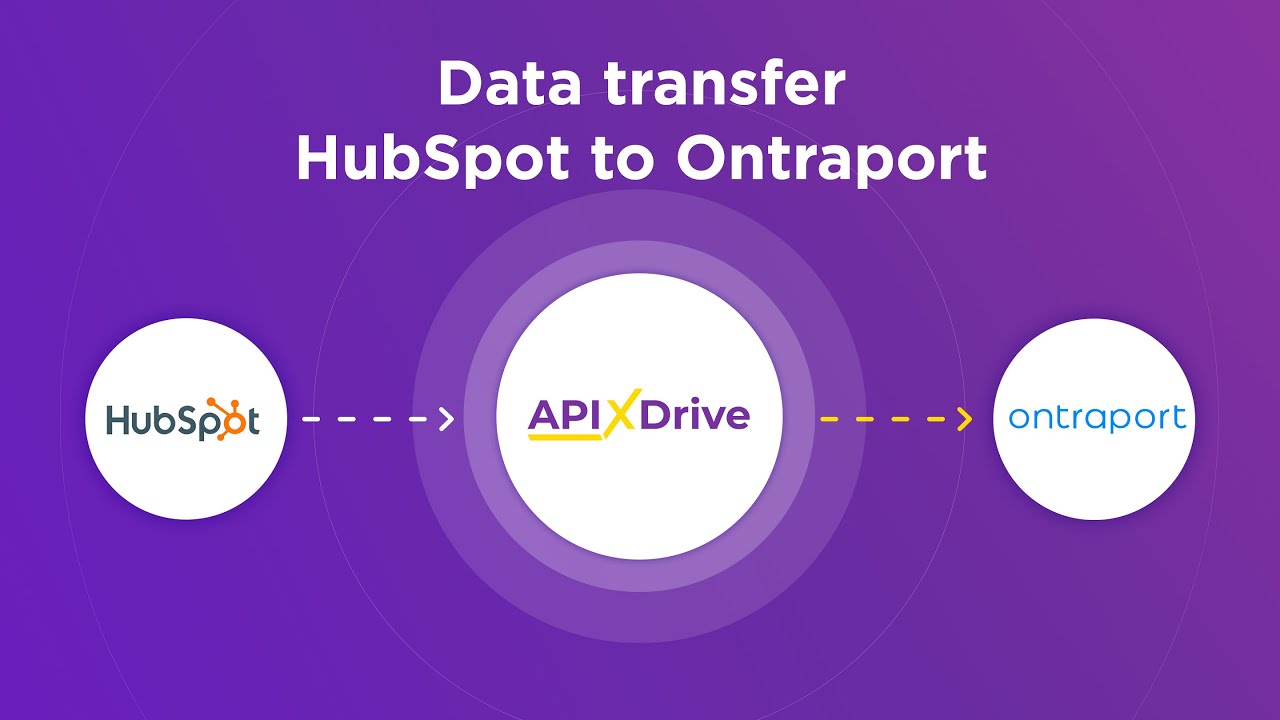
Future Trends in Manufacturing Automation Platforms
As manufacturing automation platforms continue to evolve, a significant trend is the integration of artificial intelligence and machine learning to enhance decision-making processes. These technologies enable predictive maintenance, optimizing production schedules, and improving quality control by analyzing vast amounts of data in real-time. Additionally, the adoption of IoT devices is increasing, allowing for more connected and responsive manufacturing environments. This connectivity facilitates seamless communication between machines, leading to more efficient operations and reduced downtime.
Another emerging trend is the emphasis on interoperability and integration capabilities within manufacturing automation platforms. Companies are seeking solutions that can easily integrate with existing systems and third-party services. Platforms like ApiX-Drive are becoming crucial as they provide streamlined integration services, enabling businesses to connect disparate systems effortlessly. This trend towards enhanced connectivity and integration is driving the move towards more flexible and scalable manufacturing solutions, allowing companies to adapt quickly to changing market demands and technological advancements.
FAQ
What is a Manufacturing Automation Platform?
How does a Manufacturing Automation Platform benefit a company?
Can a Manufacturing Automation Platform integrate with existing systems?
What are the key features to look for in a Manufacturing Automation Platform?
How can a company implement a Manufacturing Automation Platform?
Apix-Drive is a simple and efficient system connector that will help you automate routine tasks and optimize business processes. You can save time and money, direct these resources to more important purposes. Test ApiX-Drive and make sure that this tool will relieve your employees and after 5 minutes of settings your business will start working faster.