Data Integration in Manufacturing
Data integration in manufacturing is revolutionizing the industry by enabling seamless connectivity and real-time data exchange across various systems and processes. This integration enhances efficiency, reduces operational costs, and drives innovation by providing a unified view of production data. As manufacturers increasingly adopt digital technologies, understanding and implementing effective data integration strategies becomes crucial for maintaining a competitive edge.
Introduction
In the era of Industry 4.0, data integration in manufacturing has become a pivotal aspect for enhancing operational efficiency and decision-making processes. The seamless flow of information across various stages of production not only optimizes resource utilization but also ensures real-time monitoring and control. By integrating data from diverse sources, manufacturers can gain valuable insights, predict potential issues, and implement proactive measures.
- Improved data accuracy and consistency
- Enhanced collaboration across departments
- Real-time tracking and monitoring
- Predictive maintenance and reduced downtime
- Better compliance with industry standards
As the manufacturing landscape continues to evolve, the importance of robust data integration frameworks cannot be overstated. Companies that invest in advanced data integration technologies are better positioned to respond to market demands, innovate rapidly, and maintain a competitive edge. Effective data integration strategies are essential for driving productivity, ensuring quality, and achieving sustainable growth in the manufacturing sector.
Challenges of Data Integration in Manufacturing
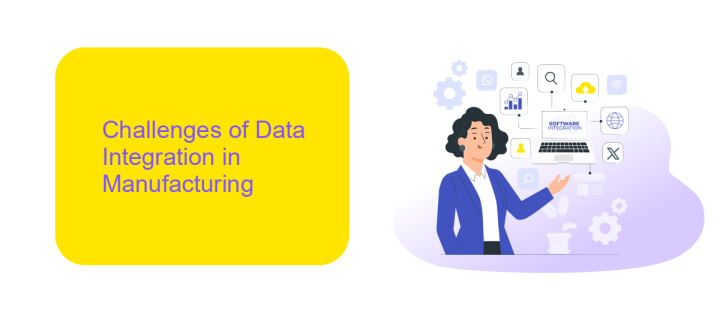
Data integration in manufacturing presents several challenges, primarily due to the complexity and diversity of data sources. Manufacturing environments typically involve numerous systems, such as ERP, MES, and SCADA, each producing vast amounts of data in different formats. Harmonizing this data to create a unified view is a daunting task, often requiring significant time and resources. Additionally, legacy systems, which are still prevalent in many manufacturing settings, may lack the compatibility needed for seamless integration, further complicating the process.
Another significant challenge is ensuring data accuracy and consistency across integrated systems. Inaccurate or inconsistent data can lead to erroneous insights and decision-making, potentially affecting production efficiency and quality. Tools like ApiX-Drive can help mitigate some of these challenges by providing automated data integration solutions that connect various systems and standardize data formats. However, even with advanced tools, ongoing maintenance and monitoring are essential to address data discrepancies and ensure the reliability of integrated data streams.
Benefits of Data Integration in Manufacturing
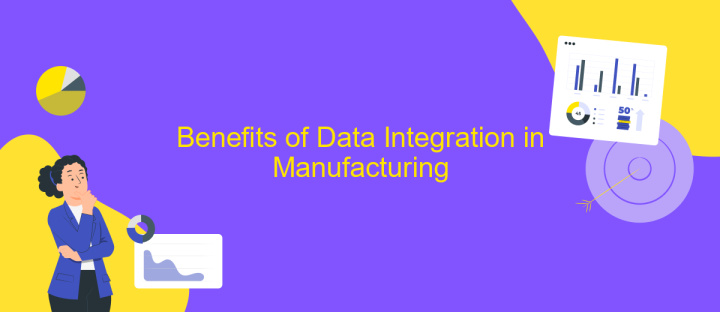
Data integration in manufacturing plays a pivotal role in enhancing operational efficiency and decision-making processes. By consolidating data from various sources, manufacturers can gain a comprehensive view of their operations, leading to improved productivity and reduced downtime.
- Enhanced Decision-Making: Integrated data provides real-time insights, enabling managers to make informed decisions quickly.
- Cost Reduction: Streamlined operations and predictive maintenance help in minimizing unexpected breakdowns and associated costs.
- Quality Improvement: Consistent data flow ensures better quality control and adherence to industry standards.
- Increased Agility: With a unified data framework, manufacturers can swiftly adapt to market changes and customer demands.
- Better Compliance: Integrated data aids in maintaining regulatory compliance by providing accurate and timely reports.
Overall, data integration fosters a more connected and responsive manufacturing environment. By leveraging integrated data, manufacturers can achieve greater operational excellence and maintain a competitive edge in the market.
Data Integration Best Practices for Manufacturing

Effective data integration in manufacturing is crucial for optimizing operations, enhancing productivity, and ensuring seamless communication between various systems. To achieve this, manufacturers must adopt best practices that facilitate accurate, timely, and secure data exchange across the enterprise.
One essential practice is to implement a robust data integration platform that supports various data formats and protocols. This platform should be capable of handling large volumes of data and ensuring real-time synchronization between systems. Additionally, it's important to establish clear data governance policies to maintain data quality and consistency.
- Utilize standardized data formats and protocols to ensure compatibility.
- Implement real-time data synchronization to avoid delays and discrepancies.
- Establish comprehensive data governance policies for data accuracy and security.
- Invest in scalable infrastructure to handle growing data volumes efficiently.
- Conduct regular audits and updates to maintain system integrity.
By adhering to these best practices, manufacturers can create a cohesive data ecosystem that supports informed decision-making, enhances operational efficiency, and drives innovation. This approach not only improves current processes but also lays the foundation for future technological advancements in the manufacturing sector.
Conclusion
In conclusion, data integration in manufacturing is a critical component for achieving operational efficiency and enhancing decision-making processes. By seamlessly connecting disparate data sources, manufacturers can gain real-time insights, streamline workflows, and reduce operational costs. The adoption of robust integration platforms and tools is essential for overcoming the challenges associated with data silos and ensuring data consistency across the enterprise.
Services like ApiX-Drive play a pivotal role in simplifying the integration process by providing user-friendly interfaces and automated data synchronization capabilities. These solutions enable manufacturers to effortlessly connect various software applications, ensuring smooth data flow and enhancing overall productivity. As the manufacturing landscape continues to evolve, leveraging advanced data integration solutions will be key to staying competitive and driving innovation.
FAQ
What is data integration in manufacturing?
Why is data integration important for manufacturing?
What types of data sources are typically integrated in a manufacturing setting?
How can manufacturers ensure successful data integration?
What tools can help with data integration in manufacturing?
Time is the most valuable resource in today's business realities. By eliminating the routine from work processes, you will get more opportunities to implement the most daring plans and ideas. Choose – you can continue to waste time, money and nerves on inefficient solutions, or you can use ApiX-Drive, automating work processes and achieving results with minimal investment of money, effort and human resources.